Most professionals in our industry understand the concept of treating the whole house as a system. Our normal focus is on insulation and air sealing, high-efficiency equipment, and good ventilation. Many contractors concentrate on the "high" and forget the "low"; attic insulation is given top priority while crawl spaces and basements are all but forgotten. Basements and crawl spaces are the foundation of the home, and problems there must be addressed when considering whole-house solutions.
We do not strictly control Google ad content. If you believe any Google ad is inappropriate, please email us directly here.
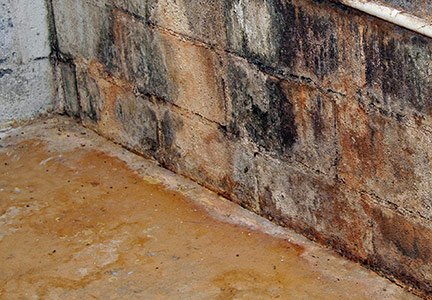
When discussing basements and crawl spaces, I like to ask people to think about the opposite—and probably more familiar—end of the house: the attic. A good attic has insulation and proper air sealing. It sometimes holds mechanical equipment, it needs to protect that equipment from the elements, and it also protects the rest of the house. Everyone understands the importance of a roof—it keeps out the water. All these things are true of basements and crawl spaces as well.
I understand the reluctance of some weatherization agencies and home performance contractors to consider fixing basements and crawl spaces. It can be difficult. There can be added liability if moisture issues are not dealt with properly. But it can be very necessary work, and it fits well within the mantra of our industry: making homes energy efficient, healthy, and safe. (See "The Scary Crawl Space," HE Jan/Feb '11, p. 38; and "Closed Crawlspaces Do Double Duty," HE 2005 special issue: "The Best of Building Performance," p. 32.)
Every GreenHomes America location that deals with crawl spaces and basements brings a home performance attitude to problems and solutions. They deal with bulk moisture; they install vapor barriers; and they insulate and air seal at the rim, between the underfloor space and the interior space, and/or at the foundation walls. If there are mechanical systems in these spaces, duct replacement or sealing and insulation may be called for. Often HVAC systems have been exposed to moisture or otherwise taxed in these under-floor spaces. If so, perhaps they should be replaced. Even when moisture is not the first concern, indoor air quality (IAQ), system longevity, and efficiency may be. Bringing these systems into the building envelope can solve many problems.
This Is Not New Construction
The best time to take moisture reduction measures is during new construction. These measures may include installing perimeter drains at the footings of foundation walls; replacing slow-draining clay around the foundation with soil that does drain; ensuring proper grade; waterproofing walls; creating drainage planes—all those things that architects and engineers draw in books. In retrofitting homes, installers face many moisture problems that cannot be solved so readily. It is too late, or prohibitively expensive, to take many of the measures outlined above. In short, addressing these moisture problems would be much easier if we were starting from scratch.
The curious thing about homes that have done just fine over many years, surviving less than ideal conditions at the foundation, is that they sometimes experience trouble when we start to improve them by air sealing and insulating. This is especially true when we disregard moisture problems. Many New England homes that have sheltered people effectively for well over 100 years were built over standing water. The seasonal wetting and drying of parts of the home comes with the territory. Once the homes are insulated and tightened up in an effort to reduce energy costs or to increase comfort, the potential for moisture problems increases. In many very old homes, temporary steel columns were installed when the home was last retrofitted (with insulation and possibly air sealing) 20-30 years ago. I find it interesting that these columns are often rusting away and in need of replacement. Yet the home survived for 100 years before it was tightened and insulated, without any supports at all. Certainly age is a factor, but often, well-intentioned contractors and homeowners have fundamentally changed how the home worked—for the worse—by ignoring the moisture dynamics in a retrofitted home.
Keeping Moisture Out from the Outside
Keeping moisture out from the outside of the house is a simple concept, but I have spent my fair share of time standing outside in the rain watching water make its way down to the foundation because a few things—such as gutters—were out of place, or because the grading was done improperly or not at all.
Some of this we have no control over; after all, this isn't new construction we are talking about. But we can and should make recommendations to address water intrusion into under-floor spaces. Look for clear signs that indicate the risk of water entering the basement. Examples include downspouts terminating too close to the house and roof runoff cutting into the ground. In both cases, water is unintentionally directed toward the foundation, greatly increasing the risk of water intrusion into the basement.
The solution could be landscaping that moves water away from the walls and/or light carpentry, such as fixing a broken gutter on a roof. Fix, or recommend that someone else fix, the easy stuff first. At the same time, I would not recommend dealing with moisture problems from the outside when to do so would entail heavy excavation. That is very disruptive, and it can be costly. There may be situations where heavy excavation is necessary, but I feel that most moisture problems can be addressed in less invasive ways.
You Can't Fight Mother Nature: Keep It Moving
Sometimes rainwater coming off the roof can't be kept out of the basement or crawl space from the outside. Sometimes the problem is caused by a high water table that is made worse when it rains. If there is evidence that someone has tried to solve water problems by filling cracks, the crack is probably not the direct cause of the problem. Foundations normally aren't built to be dams holding back a lake. Hydraulic cement and some interior paints that can stave off the inevitable for the short term do just that—stave off the problem for the short term. They are treating the symptom, not the disease. If there are no appropriate measures in place to deal with bulk water from the inside, maybe it should be allowed to come inside, and then be directed back out and away from the home.
Draining to daylight is the ideal solution, but more often than not, removing water from basements and crawl spaces means collecting and pumping. Perimeter drains can be cut into the foundation (or dirt) floor, or installed where the wall and floor intersect. A sump well can be dug to collect water.
Dealing with Vapor
Moisture problems in an under-floor space may not be caused by bulk water. They may be caused by airflow that carries water vapor into the walls and through the slab. When this happens, structural damage can happen slowly over time. By the time the damage is noticed it is often too late.
Appropriately called rising damp in the U.K., capillary action occurs in walls and floors. Moisture problems unseen at the surface level can be identified on slab or dirt floors by laying down a piece of plastic and leaving it overnight or, depending on the severity of the problem, even for a few hours. It is possible to move a box aside to reveal the moisture underneath it. Capillary action occurs in concrete as well as in other porous materials, such as wood and plaster. Surface tension and attraction on a molecular level moves the moisture until it reaches the plastic—or for that matter, the box—which acts as a condensing surface.
Earth-floored spaces may seem to be dry on the surface, only because moisture may quickly evaporate off the surface. As with concrete floors, a significant unseen source of moisture may exist. It is simple enough to scrape at the surface to see if it is moist below. Adding a vapor barrier over a dirt floor can help with the indoor air quality and will decrease the airflow from the crawl-space into the home.
Some contractors feel that a vapor barrier should not be added to a floor that may already have a vapor barrier under it. A double vapor barrier can pose problems in a wall made of organic material that is susceptible to moisture, such as wood. A wall that is not allowed to dry to one side will rot from the inside if moisture gets in but has little opportunity to get out. Air transported moisture can make its way into a cavity, condense and then compromise the wall from the inside. Concrete isn't susceptible to decay from standing water, so a double vapor barrier above and below a concrete floor will not pose problems. Whether or not the existing floor material is earth or concrete, the primary objective is to leave the moisture behind to protect the inhabitants of the building and the building itself.
Plastic makes a great long-term barrier, and while it is most often used for crawl spaces, it can be used in some basements as well. The most difficult part can be attaching it to the walls. There are plastic fasteners, adhesives and tapes, and wood straps over the material fixed with more-traditional concrete fasteners.
The simplest, quickest, and safest application would be to attach the barrier material to the wall with caulk or adhesive. The biggest downside here is ensuring that the material will stick and stay stuck. A material that is designed to install with caulk works best, as it has the plastic barrier on only one side, leaving a backer that takes adhesive very well.
This method commits the installer to attach the vapor barrier to a wall and requires a consistent wall surface. In particularly old homes, the wall could be stacked stone. While a plastic barrier could be installed on a stacked-stone wall, it would be more difficult, and the barrier would need to be finished with spray foam.
When the space is short, it may not be necessary to use a separate wall material. Sometimes installation will go quicker if it is laid out with the floor piece going up the wall. This means that adhesives must be backed up with a mechanical fastener. A safe and fairly effective method is to apply butyl tape to the wall and support it with tap fasteners. Strapping and powder-actuated nails can also be used to fasten barrier material to the walls. This is a riskier method, since the nails are driven by a small explosive charge in an enclosed space, and into concrete or block that can blow apart.
All three methods are okay, and some work better in one situation than in another. To some degree, the choice is up to the installer, who should consider what is best for the job at hand.
Good-quality reinforced polyethylene plastic 12 mil or greater is the ideal barrier material for most spaces. Use thicker plastics in high-traffic areas. I prefer to use a combination of thicknesses, depending on where the material is installed. I'll use a thinner material on a wall, or possibly a material designed to be used with adhesives. I use thicker materials on floors. Plastic rolls come in various widths. It is best to lay out the plastic with as few seams as possible. In crawl spaces, it may save time to hang one piece as a perimeter skirt and then tie it into the floor pieces with tape or otherwise seal the seams. You'll need to wrap structural posts, unless you can lift them easily and slide the plastic under them. This is important when the post is made of wood and there is no block underneath it to tie the barrier to. Installers should be comfortable with this procedure, and should understand what they are lifting when they lift the posts this way. For most seams, a good wide tape will seal plastic to plastic quite well. An overlap of 1 foot, taped together, goes on quickly and stays put.
If there is standing water in the crawl space, address this problem before you lay down plastic. I do not trust a taped seam to hold well in standing water. In a pinch you can use mastic—normally used for duct sealing—to bond the seams. It may provide a more durable installation than tape, but in my opinion, standing water should be addressed before a vapor barrier is installed.
With a basement, the vapor barrier can be laid and a slab poured over it. Pouring a new slab is a wonderful way to protect the vapor barrier, but this is clearly a big job; you should carefully consider other moisture management strategies before you take this step. A new slab is not a practical solution in many spaces because it reduces the available height of the space, since it raises the floor by 3 or 4 inches.
Insulate in the Right Places to Keep the Home Warm, Cool, and Dry
Specialists who deal with drainage and vapor barriers can miss the bigger picture. Insulation is one area that they often ignore Stuffing some fiberglass in the band joist as an. afterthought is not best practice.
In heating-dominated climates, insulation at the rim joist or perimeter wall is particularly beneficial in keeping a home warm and dry. Most of the time, closed-cell spray foam is used, but a combination of foam board and spray foam or even fiberglass can be an effective insulator. However, it can be difficult to install fiberglass in a rim joist. It takes some practice and skill to fill a cavity properly, and the temptation to stuff it in there is strong. I do not recommend using fiberglass as a wall covering in a basement or crawl space. The temptation to use the material to save on costs is real, but without a proper air barrier the insulation is ineffective. Fiberglass draped over a wall will not stop airflow. A continuous air barrier is needed. Without the air barrier, fiberglass creates a situation where the foundation wall becomes a relatively cool condensing surface for the warmer air in the space.
Another benefit of closed-cell spray foam insulation is that it can also act as an anchor for a vapor barrier. And if the insulation is tied together with the vapor barrier, it can act as part of the drainage plane. When the primary moisture problem is condensation, air sealing and insulation at the rim joist and perimeter wall help to reduce condensation in the summer months, since insulation keeps the joist and wall from acting as a condensing surface. With spray foams it is important to check the local codes, which may require the addition of an ignition barrier.
One issue in using spray foam to air seal and insulate in a subgrade space is termite control; an inspection strip is required in certain parts of the country. Some contractors cut this out after insulation has been installed, and some leave a piece of hardened insulation in place to be removed after the spray foam cures. Some spray up to a point and then insulate with another material that can be easily removed. My preference is not to leave any area uninsulated, but I recommend following the local code.
It is most important not to direct moisture up to the sill. Although it would be convenient to use the sill as an attachment point, vapor barriers should never be brought up to the sill, but should be left a few inches short of it. Attaching the barrier to a wooden sill could direct moisture from the underside of the barrier toward the wood, causing it to rot.
The bond created between spray foam and foundation walls can be compromised by the presence of dirt and moisture on the wall, or by a sharp temperature difference between the wall and the spray foam as it cures. In a way, this imperfection can be an advantage. Where there is a moisture problem in a wall, and water makes its way in, the fact that the spray foam does not adhere tightly to the wall allows the cured foam to act as a drainage plane. The foam will bond well to the plastic, so that during curing it grabs the vapor barrier and takes it with it as it cures, leaving a space between the foam and plastic and the wall for infiltrating water to make its way to the floor. As long as the vapor barrier and spray foam is continuous, moisture trapped beneath this layer will cause no problems.
Spray foam is a great solution on irregular walls in particular. If the space is a poured foundation wall it may be less expensive and simpler to use rigid board insulation such as polyisocyanurate or expanded polystyrene foam. Keep in mind the size of the access to the space you will need to bring in sheets of insulation.
Venting
Is the house you are working on by the coast of Maine or the coast of California? What about North Carolina? Clearly climate plays a role when it comes to moisture, and local codes will too.
Does it matter if it's a crawl space or a basement? In some places I don't think so, but the code does.
In hot-humid and mixed climates, as well as in coastal environments, humidity can be a problem in basements or crawls due to ventilation. Warm, humid air reaches the soil and framing members at a significantly cooler temperature than the air outside the space and this creates condensing surfaces. The ground and walls may already be damp under the first floor in these environments; introducing moist, warm air will only make it worse. (See "What the Code Says" for more on ventilation.)
Closing vented crawls (and leaky basements, for that matter) can do a great deal to control airflow. Often there is little air sealing at the first floor, and the pressures are greatest at this level. It is the "fresh"-air intake for the building's natural stack effect. An added insulation layer of spray foam acts as a good air barrier; it also reduces temperature swings, keeping condensation from forming. Rigid board works well too, especially when it is taped or otherwise sealed at the seams.
Even though the space is being effectively brought into the larger building envelope, air sealing at the first floor still makes for better IAQ as well as comfort. Air sealing ductwork is beneficial as well.
Drying, Perm Ratings, and So On
Some contractors hesitate to recommend insulation materials for walls in underfloor spaces. Building scientists have recommended that a wall be able to dry to the inside in a crawl or basement, because it won't dry to the outside—at least where the outside is below ground—but I don't think this is a critical consideration.
Because of the great potential for wetting, materials applied to the interior wall should be water resistant. Foam board and closed-cell spray foam both meet this requirement. Less than 2-3 inches of closed-cell spray foam may still be semipermeable but, like slabs, concrete, and block walls, as well as stone, it does just fine getting wet. The issue to be concerned with is whether or not the moisture reaches the sill, something we certainly don't want to see wet. I do recommend making sure that a wall be able to dry to the outside above grade in order to minimize the amount of moisture that reaches structural wood.
Concrete, being fairly porous is quite capable of carrying moisture some distance up a wall. Internal footing drains will help to relieve the pressure and deliver the water to a drain or pump. Capillary action from the soil to the concrete can really be addressed only by a well-installed and sealed vapor barrier.
Why Mess with Basements and Crawl Spaces?
I think of home performance professionals as those who take care of all the spaces that have been left behind by others. We are the ones who correct those forgotten places in the house where someone once said "good enough," backed out, and left a problem—whether or not they realized it—for someone else to fix.
At GreenHomes America we sell comfort. Making a home more comfortable is the best reason to upgrade insulation, or to improve a cooling or heating system. It is also the best reason to improve crawls and basements. Besides handling moisture better, homes with well-sealed, insulated, and ventilated basements and crawl spaces smell better—and you can bet that means they are healthier as well. The last thing we need after our efforts to tighten and insulate homes is to leave behind mold, and the health problems that go with it, for the occupants.
Author: Jason Todd is home performance training manager for GreenHomes America, a national, single-source home performance contractor with a whole-house approach that provides HVACR and building envelope solutions. He is a BPI-certified Analyst and Envelope Professional and proctor.
Reprinted by permission of Home Energy magazine.
HHI Error Correction Policy
HHI is committed to accuracy of content and correcting information that is incomplete or inaccurate. With our broad scope of coverage of healthful indoor environments, and desire to rapidly publish info to benefit the community, mistakes are inevitable. HHI has established an error correction policy to welcome corrections or enhancements to our information. Please help us improve the quality of our content by contacting allen@healthyhouseinstitute.com with corrections or suggestions for improvement. Each contact will receive a respectful reply.
The Healthy House Institute (HHI), a for-profit educational LLC, provides the information on HealthyHouseInstitute.com as a free service to the public. The intent is to disseminate accurate, verified and science-based information on creating healthy home environments.
While an effort is made to ensure the quality of the content and credibility of sources listed on this site, HHI provides no warranty - expressed or implied - and assumes no legal liability for the accuracy, completeness, or usefulness of any information, product or process disclosed on or in conjunction with the site. The views and opinions of the authors or originators expressed herein do not necessarily state or reflect those of HHI: its principals, executives, Board members, advisors or affiliates.